Allegiant Solutions Casing Chronicles
July 2025 Edition
WE'VE BEEN WORKING ON SOMETHING.
It's not new to the world - but it's new for us. We've taken a proven concept and applied it to one of our most widely used threads, creating something purpose-built for reliability.
Coming soon…


PUSH FOR BETTER
In June, Team Allegiant took on The Push-Up Challenge — not just for fitness, but to support mental health awareness across Australia. Over a few active weeks, we pushed through reps to raise funds for The Push For Better Foundation and start meaningful conversations.
​
From the workshop to the field, everyone got involved — and rumour has it Kieran may have even squeezed in a few push-ups underground!
ON-SITE PERFORMANCE THAT SPEAKS FOR ITSELF
Last month, our AS-AH thread from the A-Series range proved its strength out in the field. Designed for demanding jobs, this flush joint casing delivered real results on site:
✔ Faster installs
✔ Reduced rig time
✔ No hot work near the hole
✔ Strong, secure joints under load
With certified welds and full traceability, it’s a smart, field-tested solution built to perform.
Want to see more? Take a look at the full A-Series range.

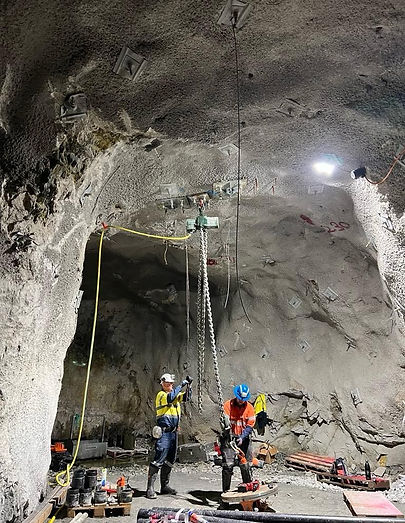
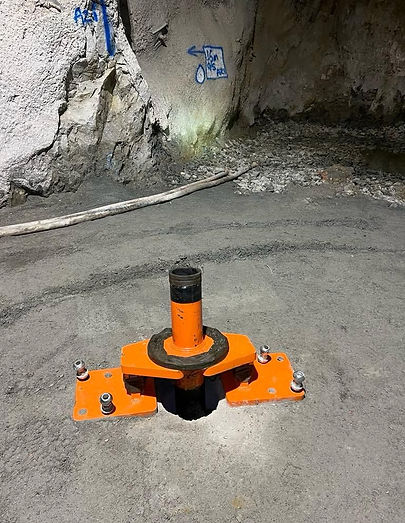
UNDERGROUND EXCELLENCE: LUKE AND KIERAN IN ACTION
While snow and sleet hammered the surface, our team stayed focused where it mattered most—below ground.
Luke Nelson and Kieran Chiverton are back on the road, taking on the underground challenge with exceptional precision. On a recent casing install, they delivered outstanding running times despite the harsh conditions. Their commitment and efficiency are a true reflection of what Allegiant stands for.
Tough conditions. Standout performance. That’s Allegiant in action.
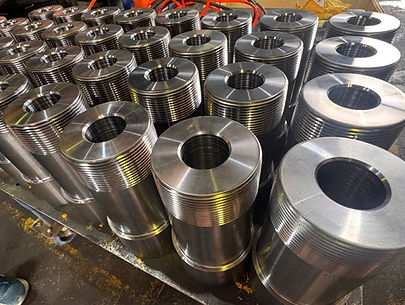
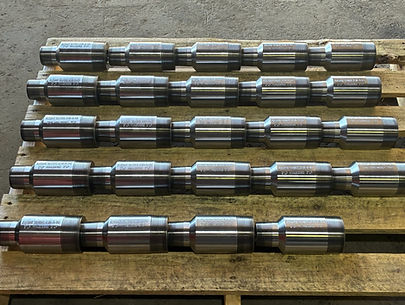
CUSTOM WORK, THE ALLEGIANT WAY
Our machine shop was busy turning out more than just casing — we had the opportunity to produce a specialty run of 3" Line Pipe Male × 2" Line Pipe Male swages for one of our long-time clients. These weren’t off-the-shelf parts, but that’s exactly where our in-house machining capabilities shine.
The material was imported, precisely machined on-site, and prepped for phosphating — all handled with the same attention to detail and quality we bring to every job.